Here’s the mounting hardware that was “grown†to hold in place the power indicator LED. The holder was designed to allow for positioning the LED relative to the faceplate as shown in the following photos. It's made from polycarbonate using a technique named fused deposition modeling (FDM).
For those that are interested here is an excerpt from the color glossy of the system used to make this part:
"FDM begins with a software process, developed by Stratasys, which processes an STL file (stereolithography file format) in minutes, mathematically slicing and orienting the model for the build process. If required, support structures are automatically generated. The machine dispenses two materials – one for the model and one for a disposable support structure."
"The thermoplastics are liquefied and deposited by an extrusion head, which follows a tool-path defined by the CAD file. The materials are deposited in layers as fine as 0.04 mm (0.0016") thick, and the part is built from the bottom up – one layer at a time."
"FDM works on an "additive" principle by laying down material in layers. A plastic filament or metal wire is unwound from a coil and supplies material to an extrusion nozzle which can turn the flow on and off. The nozzle is heated to melt the material and can be moved in both horizontal and vertical directions by a numerically controlled mechanism, directly controlled by a computer-aided manufacturing (CAM) software package. The model or part is produced by extruding small beads of thermoplastic material to form layers as the material hardens immediately after extrusion from the nozzle. Stepper motors or servo motors are typically employed to move the extrusion head."
"Several materials are available, such as acrylonitrile butadiene styrene (ABS) polymer, polycarbonates, polycaprolactone, polyphenylsulfones and waxes, with different trade-offs between strength and temperature properties. A "water-soluble" material (such as PVA) can be used for making temporary supports while manufacturing is in progress, this soluble support material is quickly dissolved with specialized mechanical agitation equipment utilizing a precisely heated sodium hydroxide solution."
I plan on using RTV as an adheasive to mount this to the back side of the faceplate as I did not want to modify the beautiful faceplate.
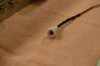